We work hand in hand with our clients to develop and evolve products over time
Research, develop and grow with us
The Domel team undergoing advanced logistics training in Poznan
A course in advanced logistics training was held from 26 to 28 April in Poznan, Poland. The training is an integral part of the activities planned as part of the NEXTLOG project, of which Domel is a partner. It was attended by Gašper Gašperšič from the supply chain planning department, Tjaša Šolar from developmental logistics and Benjamin Seljak, warehouse manager.
Fig 1: Training participants (photo: WSL)
The aim of the training was to test the usefulness of logistical content that had been prepared by professors from Greece, Poland and Slovenia. The content was prepared to ensure the competitive competence of students who will graduate from logistics faculties in the medium term. It is also intended for the internal training of employees in companies such as Domel. The training included the following content:
1. Sustainability as a service in supply chains & the manager of the future, Jakub Brzezinski, MA, UoL
2. New technologies in logistics, Waldemar Osmólski, Ph.D., WSL, Matjaž Maletič, Ph.D., UMA
3. Intelligent logistics and transportation systems, Prof. Dilay Celebi Gonidis, Ph.D., SEERC
The event took place at the Poznan School of Logistics (WSL). The training was followed by networking among logistics experts, including a tour of the city.
Fig 2: Poznan (photo: Benjamin Seljak)
More Domel insights:
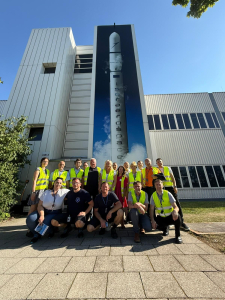
Last week, Domel took part in a professional excursion organized by the Slovenian-German Chamber of Commerce (AHK Slovenia), in cooperation with the Slovenian Space Office (Ministry of the Economy, Tourism and Sport), and under the patronage of the Bavarian Ministry of Economic Affairs, Regional Development and Energy.
Read article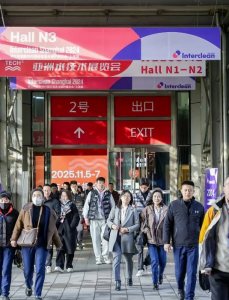
As a globally established leader in motor component, research and development, and manufacturing, Domel is committed to delivering efficient, intelligent, and eco-friendly core power solutions for cleaning equipment. With innovative technology driving industry progress, our products are widely applied in both commercial and household cleaning machines, significantly enhancing overall performance.
Read article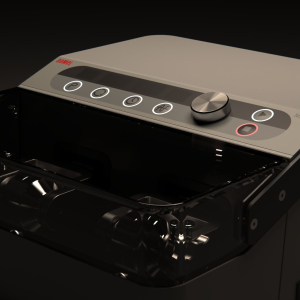
At the regional innovation awards ceremony, our laboratory mill Millmix 30 received a gold award from the Chamber of Commerce - Gorenjska Regional Office, securing its place at the national level competition.
Read article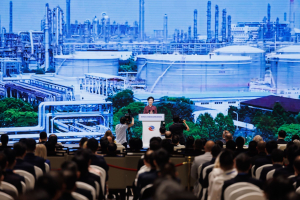
We are proud to have participated in the China–CEEC Expo 2025 in Ningbo, where Slovenia was featured as the guest of honor.
Read article